Latest Article
Comprehensive Plunger Pump Guide: In-depth Analysis of Principles, Key Components, and Selection
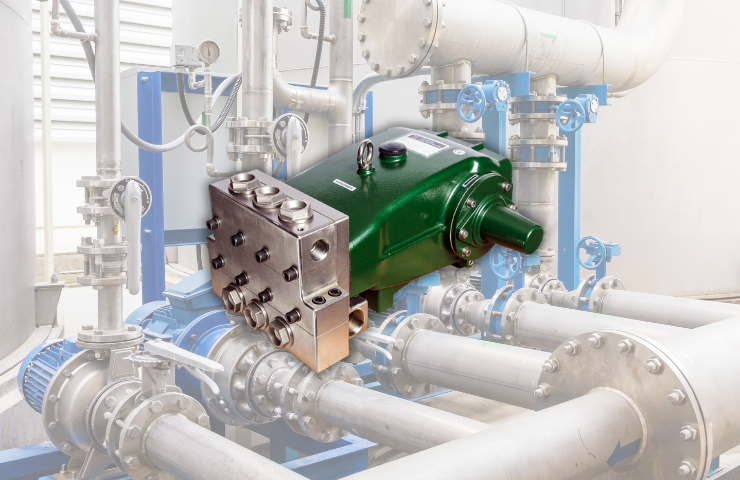
Understanding the Plunger Pump
A plunger pump, also known as a positive displacement pump, is a type of reciprocating pump that relies on a solid plunger moving back and forth within a stationary cylinder to displace and pressurize fluid. Its unique design enables it to efficiently generate and maintain high pressure.
Further Reading: Types of Plunger Pumps: Get to Know Everything about Plunger Pumps - From Basic Principles to Structure
The plunger pump plays an indispensable role in numerous high-pressure applications, including industrial cleaning, oil and gas extraction, reverse osmosis (RO) water treatment, and even precision misting, humidification systems, and agricultural spraying. Its robust and durable structural characteristics make it an ideal choice for handling such demanding operating conditions.
Basic Operating Principle of a Plunger Pump
The vast majority of plunger pumps seen in industrial applications are "force pumps." Their operational core can be broken down into two main strokes:
Suction / Intake Stroke
During this phase, the plunger moves backward (or upward) within the cylinder, causing the internal volume of the cylinder to expand and subsequently creating a partial vacuum (i.e., a pressure decrease). At this point, the higher external atmospheric pressure or the system's source pressure will push the fluid to overcome the resistance of the inlet check valve, allowing it to flow smoothly into the pump cylinder.
Discharge / Pressure Stroke
Once the suction stroke is complete, the plunger changes direction, moving forward (or downward) into the cylinder. This action compresses the fluid within the cylinder, reducing its volume and significantly increasing its pressure. When the pressure reaches a certain level, it can push open the discharge check valve, forcefully expelling the high-pressure fluid from the cylinder into the target system. Throughout this process, the inlet check valve remains tightly closed to prevent any backflow of fluid.
The Crucial Role of Check Valves
The inlet and discharge check valves are critical components ensuring the proper operation of a plunger pump. They act like one-way gates, precisely controlling the fluid to flow in only one direction through the pump (only the inlet valve opens during suction, and only the outlet valve opens during discharge). This is fundamental for the plunger pump to achieve continuous and stable pressurized fluid delivery.
Key Components and Functions of a Plunger Pump
The precise operation of a plunger pump relies on the coordinated cooperation of multiple key components. Its structure can generally be divided into two main parts: the Liquid End (or Fluid End), which directly handles the fluid, and the Power End, which provides the driving force.
Liquid End Components:
- Pump Cylinder (or Fluid Cylinder): This is the core chamber where the plunger reciprocates to achieve fluid displacement. Its design must be capable of withstanding the high pressures generated during pump operation.
- Plunger: This is a solid, precision-machined cylindrical rod that reciprocates linearly within the cylinder. Common plunger materials include:
- Ceramic: Offers excellent wear and corrosion resistance, particularly suitable for applications requiring long operating hours and handling various fluids. It's a hallmark feature of high-quality pumps (e.g., Diamond systems).
- Hardened Stainless Steel: Possesses good strength and a certain degree of corrosion resistance.
- Other Robust Alloys: Selected based on specific chemical fluids or operating conditions. The smoothness of the plunger surface is critical to the lifespan of the seals.
- Inlet and Discharge Valves (Check Valves): Typically designed as spring-loaded poppet valves or disc valves, they are used to precisely control the unidirectional flow of fluid into and out of the cylinder. The efficient operation of these valves is a direct guarantee of pump performance.
- Packing or Seals: These are crucial sealing elements installed within the stuffing box or seal housing. Common types include V-ring packing and U-cups. They form a dynamic seal between the reciprocating plunger and the stationary cylinder wall, effectively preventing high-pressure fluid from leaking out of the pump. The material and design of the seals must be selected based on fluid properties (such as chemical composition, temperature) and operating pressure.
- Stuffing Box/Seal Housing: This is a chamber structure specifically designed to house, support, and secure the packing or seals around the plunger.
- Manifold: Responsible for uniformly directing the fluid from the source to the inlet of each cylinder and collecting the high-pressure fluid from the outlet of each cylinder, then directing it to the system piping.
Power End Components:
- Crankshaft: Its primary function is to convert the rotational motion from the drive source (such as a motor or engine) into the power that drives the plunger in a reciprocating linear motion. The crankshaft is typically made of high-strength materials and supported by robust bearings.
- Connecting Rods: Responsible for transmitting the rotational power of the crankshaft (after conversion to linear motion) to the plunger (in some designs, this occurs via a crosshead).
- Crosshead (Employed in Some Designs): This is a sliding connecting piece, primarily serving to guide the plunger in precise linear motion while absorbing lateral thrust generated during operation. This reduces direct wear on the plunger and seals, and is more common in heavy-duty, high-pressure pump designs.
- Crankcase: Serves as the external housing for the power end, containing and protecting internal moving components such as the crankshaft and connecting rods. It also forms the basis of the power end's lubrication system.
Drive Mechanism:
This refers to the original power source for the plunger pump. Common drive methods include:
- Electric Motor: Most commonly used for stationary industrial applications.
- Gasoline or Diesel Engine: Suitable for mobile equipment or locations lacking a stable power supply.
Design Types and Configuration Considerations for Plunger Pumps
Plunger pumps come in a variety of designs to suit a wide range of application needs. The main classification methods include by the number of plungers, mode of action, plunger material, and drive configuration.
For detailed classification explanations, please refer to: Types of Plunger Pumps: Get to Know Everything about Plunger Pumps - From Basic Principles to Structure
Understanding Key Plunger Pump Specifications
When selecting or evaluating a plunger pump, several core specification indicators must be carefully considered: flow rate, pressure, power requirement (horsepower), and speed (RPM).
For detailed interpretations of each specification, please refer to: Introduction of Four Main Index of High Pressure Pump Specification
Furthermore, Fluid Compatibility and Temperature Limits are factors that cannot be ignored. It is essential to ensure that the pump's wetted parts materials (including plungers, seals, valves, cylinders, etc.) are chemically compatible with the fluid being conveyed and can operate stably within the expected operating temperature range.
Advantages and Limitations of Plunger Pumps
Main Advantages:
Thanks to its unique design, the plunger pump offers significant advantages in many demanding applications:
- Excellent High-Pressure Capability: Specifically designed for efficiently generating extremely high discharge pressures.
- Superior Operating Efficiency: Typically exhibits high volumetric and overall operating efficiencies (often exceeding 90% in many cases).
- Stable and Consistent Flow Rate: As a positive displacement pump, its flow rate is virtually unaffected by changes in outlet pressure within its rated operating range.
- Robust Durability and Long Service Life: Features a sturdy construction, especially models using high-quality wear-resistant materials like ceramic plungers, ensuring a long service life with proper maintenance.
- Wide Fluid Adaptability: Depending on the specific design and material selection (such as special valve designs, corrosion-resistant materials, etc.), it can handle various types of fluids, including some containing mild abrasives or those with a certain viscosity.
- Precise Flow Control: The flow rate is directly related to the pump's operating speed, allowing for precise flow control by adjusting the drive speed using methods like variable frequency drives.
Main Limitations and Considerations:
Although plunger pumps offer superior performance, their inherent limitations must be noted during selection:
- Higher Initial Purchase Cost: Compared to some other types of pumps (e.g., centrifugal pumps), the upfront investment for a plunger pump is typically higher.
- Sensitivity to Abrasives (Without Special Design): While some designs can handle fluids with mild abrasives, highly abrasive fluids will accelerate the wear of plungers, seals, and valves if the pump is not specifically designed for such conditions.
- Relatively Complex Structure and Maintenance Requirements: The structure of the power end and sealing devices is relatively complex, potentially requiring more specialized or frequent maintenance than simpler pump types.
- Size and Weight Considerations: For the same flow output conditions, a plunger pump may be larger and heavier than, for example, a centrifugal pump.
- System Requires a Pressure Relief Valve: Like all positive displacement pumps, a suitable pressure relief valve must be installed in the discharge line to prevent system overpressure from damaging the pump or piping in case of an outlet line blockage.
- Operating Noise: Compared to rotary pumps, a plunger pump may generate more noise during operation.
Operation, Maintenance, and Basic Troubleshooting of Plunger Pumps
Safe and Efficient Operation Points:
- Pre-Operation Checks: Always check if the lubricating oil level in the power end is normal, confirm all pipe connections are secure and leak-free, ensure safety guards are in place, and verify that the system's pressure relief valve is correctly set and functional.
- Priming: Before starting, ensure the pump casing is filled with the fluid to be conveyed (priming) to prevent pump damage from dry running, unless the pump itself is designed for short periods of dry running.
- Avoid Cavitation: Ensure the pump suction inlet has sufficient Net Positive Suction Head available (NPSHa) to prevent cavitation damage to the pump. This means checking that the suction line is unobstructed and its diameter is adequate.
- Operational Monitoring: During pump operation, closely monitor whether the outlet pressure and flow rate are within normal ranges, listen for any abnormal noises (such as knocking, grinding, etc.), and frequently check for any leakage.
Recommended Routine Maintenance Plan (General Guidelines - Always Refer to the Manufacturer's Specific Manual):
- Daily Inspection: Visually inspect for any fluid or lubricating oil leakage, listen for normal operating sounds, and make a preliminary judgment of vibration levels.
- Weekly/Monthly Inspection (or based on specific operating hours): Check and, if necessary, replenish or replace the crankcase lubricating oil. Inspect and appropriately adjust the packing (for adjustable designs, some packing requires slight leakage for lubrication and cooling). Check belt tension and alignment (if belt-driven). Clean the inlet filter or strainer.
- Periodic Maintenance (e.g., annually or per the manufacturer's manual recommendations): Replace the crankcase lubricating oil (using recommended specification oil). Replace worn packing/seals. Inspect valves, valve seats, and plungers for wear, and replace or repair as needed.
Conclusion
After gaining an in-depth understanding of the operating principles, key components, diverse specifications, and correct operation and maintenance methods for plunger pumps, we can more clearly recognize their core value in various industrial application fields. Whether in oil extraction, precision water treatment, or demanding chemical processes, the plunger pump plays an indispensable role in fluid conveyance and pressurization.
Through correct selection, standardized operation, and meticulous maintenance, the plunger pump can provide efficient, reliable, and durable fluid handling solutions for various industries.
If you have any further questions regarding the selection, application, or maintenance of plunger pumps, or require more detailed technical information and support, please feel free to contact us.